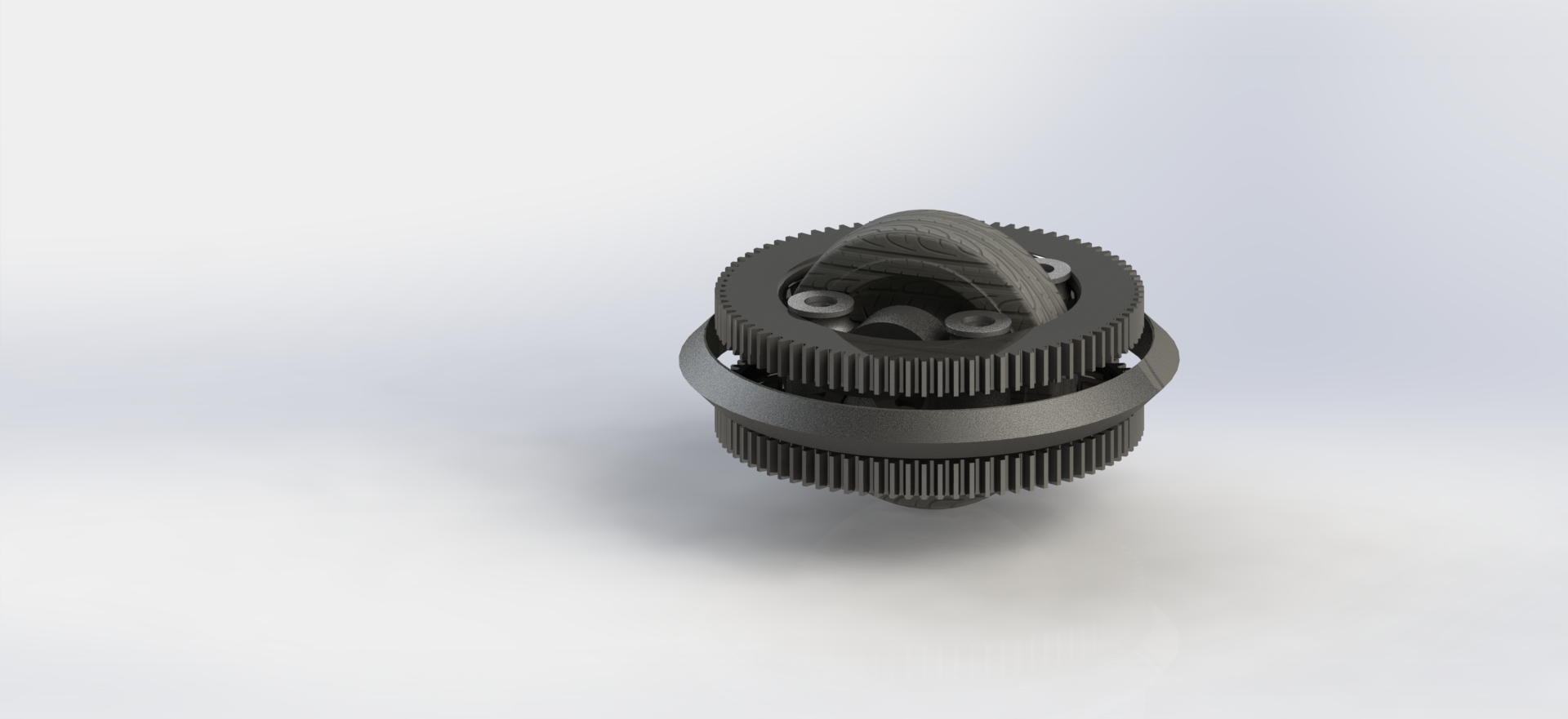
The differential gear system has long been a staple in automotive drivetrains, providing the ability to distribute torque between two wheels while allowing them to rotate at different speeds. However, recent advancements in technology have expanded its application beyond traditional vehicles. One notable innovation is the differential swerve module, which integrates the differential gear system into an omni-directional drive train, enabling wheels to rotate on two axes.
The fundamental principle of the differential gear system lies in its ability to distribute torque between two wheels while accommodating different rotation speeds. In traditional automotive applications, this mechanism prevents excessive tire wear and strain on the drivetrain during turns. By allowing each wheel to rotate independently, the differential gear system ensures a smooth and stable driving experience.
In the context of the differential swerve module, the differential gear system takes on a new significance. Through the integration of bevel gears and a rotational base, the swerve module allows a wheel to rotate around its central axis and a vertical axis simultaneously. This revolutionary design empowers the drive train to move in any direction, including lateral and diagonal movements, providing unprecedented maneuverability.
The differential swerve module comprises several key components that work together harmoniously. At its core is the differential gear assembly, consisting of bevel gears and spider gears. As the wheel rotates, these gears distribute torque between the two axes, enabling independent motion. The bevel gears transmit power from the motor to the wheel assembly, ensuring efficient power transfer. The rotational base, incorporating bearings and a sturdy support structure, enables the wheel to rotate around the vertical axis, facilitating omni-directional movement.
The integration of the differential gear system into the swerve module brings forth numerous advantages. Firstly, enhanced maneuverability is achieved, allowing the drive train to effortlessly navigate in any direction. This feature proves invaluable in fields such as robotics, autonomous vehicles, and material handling systems, where precise control and movement versatility are paramount.
Furthermore, the differential gear system in the swerve module ensures precise control over each wheel’s speed and direction. This attribute enhances stability and control during complex maneuvers, high-speed turns, and sudden changes in direction. The module’s ability to rotate on two axes provides a significant advantage over traditional drive train systems, enabling smoother and more responsive motion.
The potential applications of the differential swerve module are vast. In robotics, the module allows for omnidirectional movement, facilitating navigation through crowded environments, precise positioning, and the execution of intricate tasks. Material handling systems, such as those in warehouses and distribution centers, can benefit from the module’s ability to maneuver in tight spaces and change directions swiftly, improving operational efficiency.
In conclusion, the integration of the differential gear system into the differential swerve module has revolutionized omni-directional drive trains. By enabling wheels to rotate on two axes, this innovation has significantly enhanced maneuverability, control, and stability in various applications. The module’s ability to distribute torque and allow independent rotation opens up a world of possibilities in robotics, autonomous vehicles, and material handling systems. As advancements continue to emerge in design, control algorithms, and materials, the potential for the differential swerve module will only continue to expand, solidifying its position as a cornerstone of modern drive train innovation.